08/04/2024
The Importance of Master Samples in Quality Control
BUSINESS NEWS | 15
Understanding Master Samples in Manufacturing: Their Importance and Role
When it comes to ensuring product quality, you might encounter the concept of a ‘master sample.’
A master sample, often referred to as an approval sample, is a prototype sent by your manufacturer before initiating mass production. This sample exemplifies a product that perfectly meets your established quality benchmarks. These essential samples act as a benchmark for assessing all subsequent production items. By using master samples, you can enhance your quality control processes and effectively prevent any decline in product quality over time.
Developing Master Samples: A Comprehensive Guide
Master samples play a pivotal role in the manufacturing approval process, serving as the definitive benchmark for production quality. Here’s a detailed look at how these critical samples are developed and utilized:
The Approval Process
- Pre-Production Sample Submission
- The manufacturer prepares and sends pre-production samples to you. These samples are crafted to match your exact specifications and quality standards.
- Inspection and Feedback
- Upon receiving the samples, you meticulously inspect them against your quality criteria. This inspection covers all aspects, from material quality and dimensions to functionality and aesthetics.
- Approval or Rejection
- If the samples meet your standards, you approve them, giving the green light for mass production. If they fall short, you provide detailed feedback to the manufacturer, who then revises and produces new samples.
- Final Approval
- Once the revised samples meet all requirements, you provide final approval. This step confirms that the production can proceed.
Documentation and Distribution of Master Samples
After approval, it is crucial to document and distribute the master samples properly. This ensures consistency and serves as a reference throughout the production process. Here’s how to manage them:
- Signature and Seal
- Each master sample should be signed, dated, and sealed. This formalizes the sample as the official standard for production.
- Distribution
- Manufacturer’s Reference: One sample remains with the manufacturer to guide the production process.
- Third-Party Inspectors: Provide samples to any third-party quality inspectors who will oversee production. This ensures they have a clear benchmark for quality assessments.
- Internal Reference: Keep a sample for your records. This allows you to verify that the final products match the approved standard.
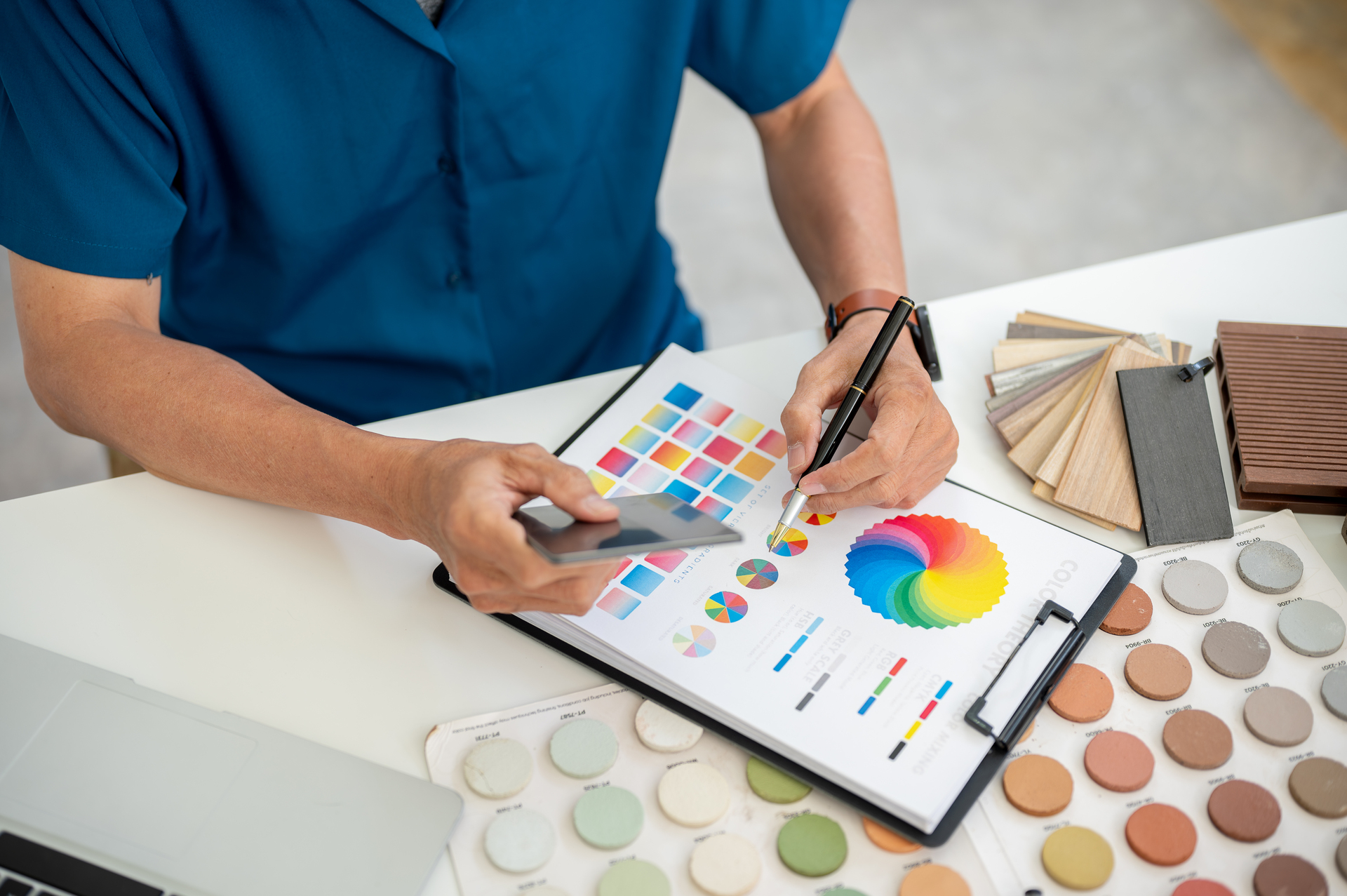
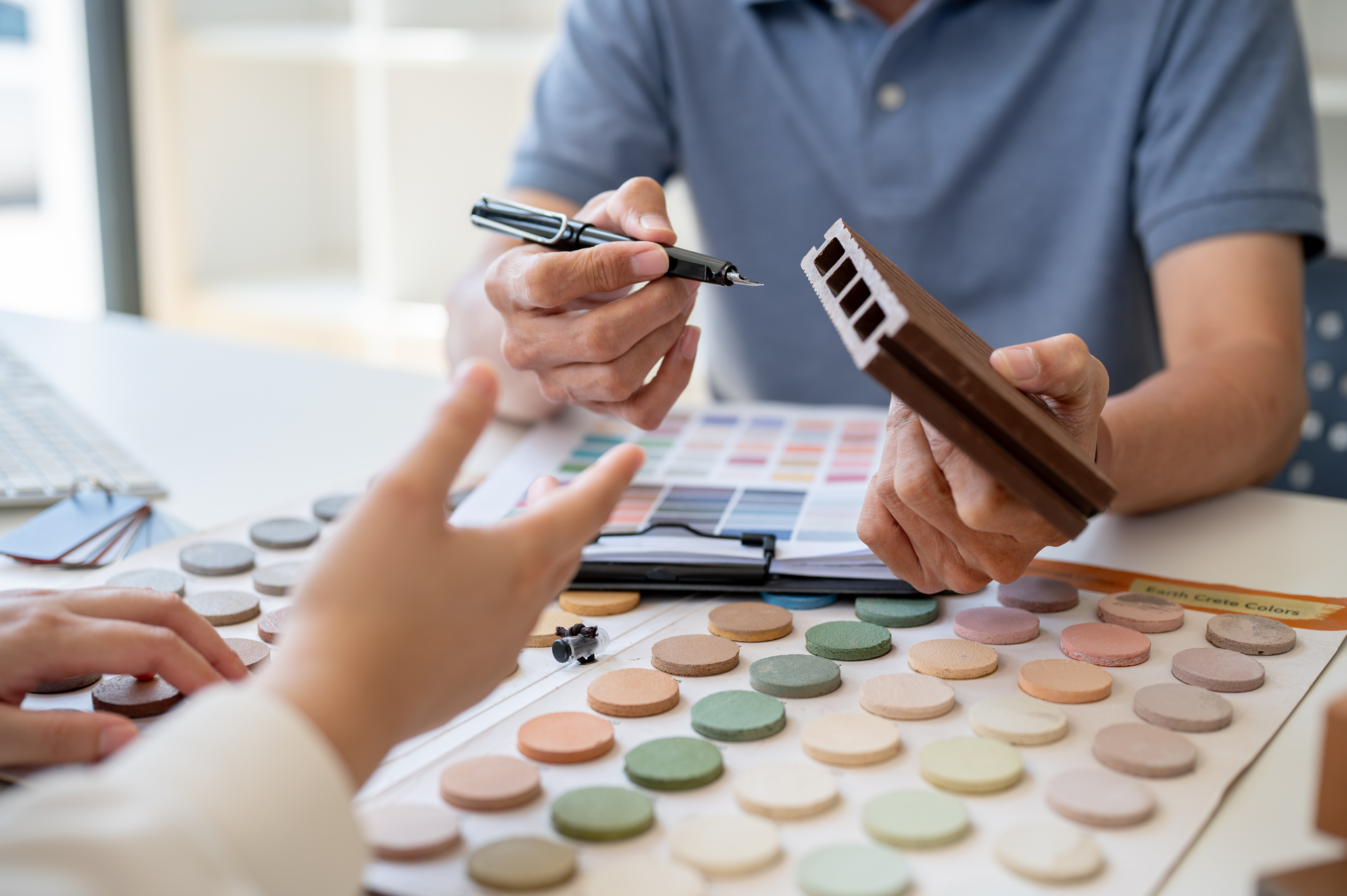
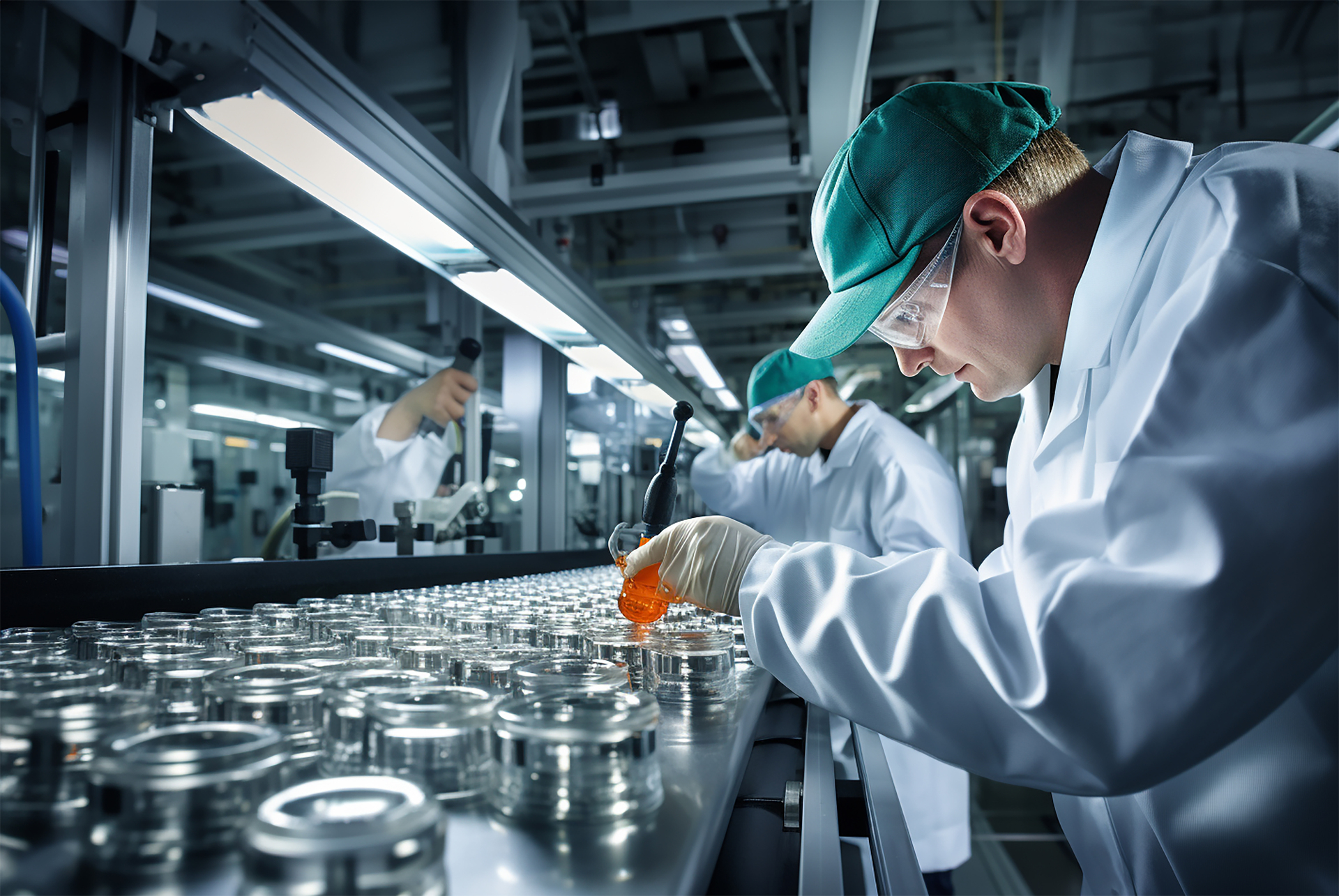
“Inspection Process Using AQL Sampling Method“
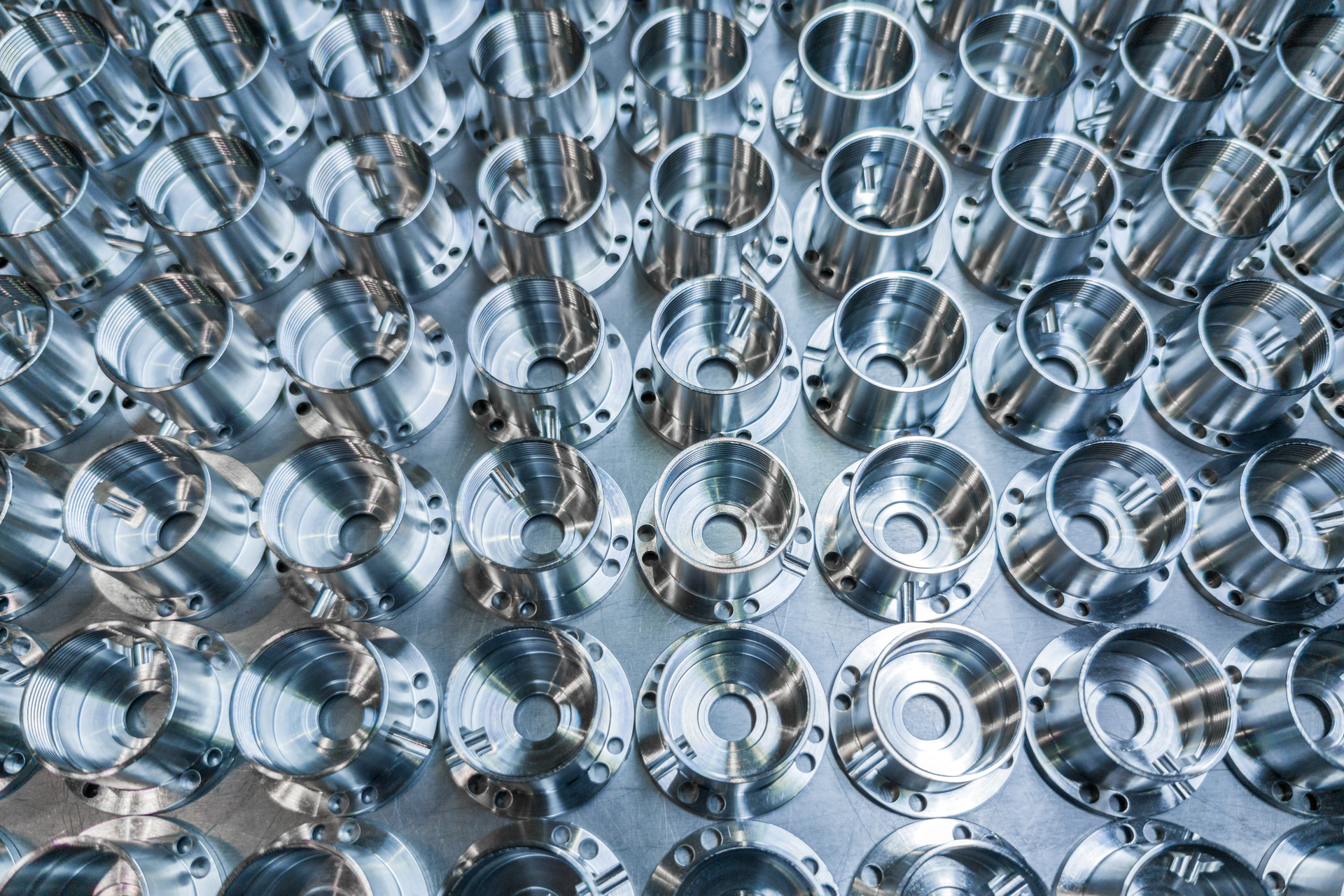
Inspection Process Using AQL Sampling Method
The inspector uses the Acceptable Quality Limit (AQL) sampling method to randomly select products from the order for inspection. This statistically-based method ensures that the sample size and selection process are unbiased and representative of the entire batch.
- Visual Inspection: The inspector visually examines the products to identify any obvious defects or inconsistencies compared to the master sample.
- Packaging and Labeling Check: The inspector verifies that the packaging and labeling meet the specified requirements, ensuring they are consistent with your brand standards and regulatory requirements.
- Physical Requirements Verification: The inspector measures and checks the physical attributes of the products to ensure they conform to the specified dimensions, materials, and other physical criteria.
- Functional Testing: The inspector tests the product functions to ensure they operate as intended. This step is crucial for items with mechanical or electronic components.
- Special Tests: Depending on the product, the inspector may conduct additional tests, such as safety tests, stress tests, or durability tests, to ensure the products meet all necessary standards and requirements.
Importance of the Master Sample Having the master sample on hand is pivotal during the inspection. It provides a clear standard for comparison, making it easier to identify deviations or defects in the production items. If any quality issues are detected, they can be immediately addressed with the manufacturing partner to find a solution before the products are shipped.
Benefits of Regular Inspections with Master Samples
- Maintaining Quality Standards: Regular inspections ensure that all products meet your established quality standards, reducing the risk of defective items reaching customers.
- Preventing Quality Issues: By identifying and resolving issues before shipment, you prevent potential returns, complaints, and damage to your brand reputation.
- Efficient Communication: The master sample serves as a clear reference point, facilitating efficient communication between you, the inspector, and the manufacturer.
- Cost Savings: Early detection of issues can save costs associated with rework, returns, and recalls, making the inspection process a valuable investment.
- Customer Satisfaction: Consistently high-quality products lead to greater customer satisfaction and loyalty, enhancing your market position and brand value.
By integrating master samples into your inspection process, you enhance the effectiveness of your quality control efforts, ensuring that every product meets your high standards and delivers the quality your customers expect.